
Leather craftsman Garvan de Bruir built his own aeronautical-inspired modular home in Kildare
Luxury leather designer Garvan de Bruir looked to the history of aeronautics when he built his innovative, experimental home, writes Serena Fokschaner.
Most creatives yearn to build their own home. Planning permitting, starting from the ground up offers the chance to experiment with materials, styles and ideas. Type “self build” in to Google and up will pop abodes ranging from the singular to the dotty. Triangular houses squeezed into tight urban spots, round houses perched on stilts like landlocked moons: the vacant plot is your blank canvas.
Garvan de Bruir’s Kildare home is a case in point. A designer-craftsman, best known for his leather bags and accessories, Garvan drew on aeronautical design to build his unusual, timber-framed dwelling. “The technical term is a ‘monocoque’, which refers to the cocooning shape of an aircraft’s fuselage,” he explains. “It’s thin but by virtue of its curved profile – like a shell – it’s also very strong.” It’s also eco-friendly: “You use the minimum amount of materials for maximum effect.”
The result is hard to miss. The “Aviator Haus” is a gleaming, hoop-shaped structure rising from flat green fields, where a low stone wall is all that remains of a former abbey. Previously a scrap yard, the site later became an industrial zone.
“Because I built my workshop here I was allowed to add a home as well,” says Garvan, who built the two-bedroom, pre-fabricated structure himself. Its pre-insulated components were digitally cut and assembled, as neatly as Lego, in sections over the course of a few weeks.
The ideas behind his “invent and build” abode grew out of Garvan’s fascination with wood and its architectural potential. He studied furniture making at Buckinghamshire Chilterns University College in High Wycombe, the former furniture-making hub of the UK. “During the Second World War, local factories also made parts for aircraft. A shortage of metal led to a return to timber. They used plywood, heavily engineered for strength. I began thinking about how I could apply those techniques to architecture. As a designer-craftsman you’re always innovating.”
His “melting pot of ideas” home was executed on a tight, self-builder’s budget… it was about materials and economy, he says. The curving outer “shell” is covered in a powder-coated, corrugated iron, rivetted like a fuselage: “It is what they use for local farm buildings, but unfortunately the planners wouldn’t allow me to use the classic agricultural red oxide colour.” For the exterior, he used cedar cladding with inexpensive PVC-framed windows.
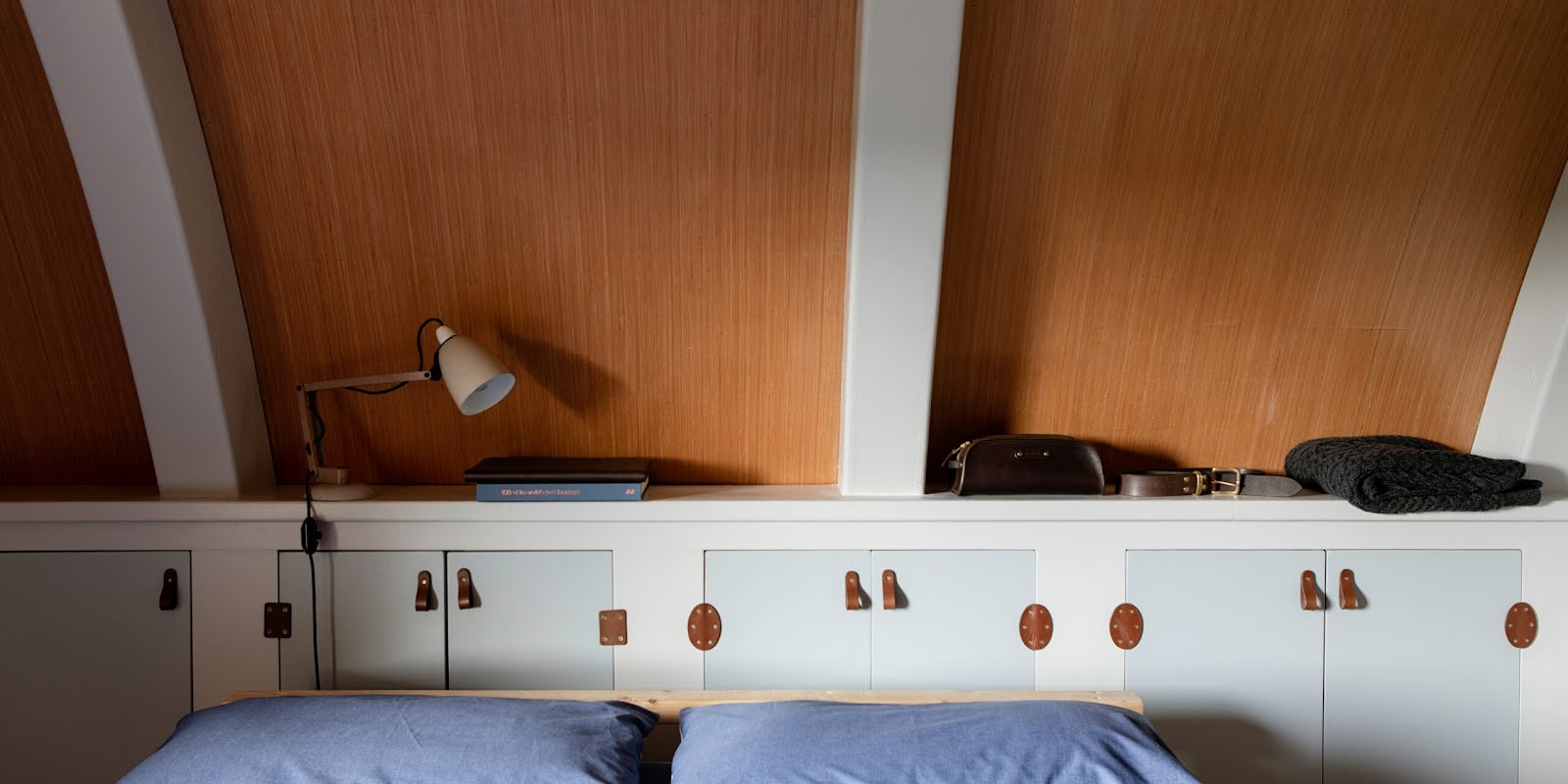
Measuring a lean five metres wide by ten metres long, there is an open-plan living area downstairs with two bedrooms and a bathroom upstairs where light spills in through windows at either end. “It’s your classic terraced house,” smiles Garvan, industrious in his leather apron.
But of course, it is not really: “In a traditional house the ceiling corners of the top-floor rooms are dead space. By eliminating them you cut down on the energy needed to heat the space,” he explains. “A typical house requires thick walls to support a heavy roof; the curved profile does away with that, reducing the materials needed.”
With its gently sloping walls and wood panelling, the interior feels as cosy as a woodland cabin, mixed with the economical elegance of a captain’s cabin. “The different woods add texture and warmth,” says Garvan, pointing out the floors, made from a budget-engineered wood (OSB) produced in Waterford. The staircase, which twirls gracefully upstairs, is made from offcuts. The walls are clad in plywood, which is also used to make the kitchen with its ingeniously curved doors and shelves of cheerful pottery.
There is leather here too in unusual details like the handles or hinges, inspired by vintage luggage design. “Leather as a building material has been overtaken by plastic or metal. But its strength and flexibility makes it so versatile,” he notes. Other “experiments” include the leather tables and chairs perched on animated, curving legs.
Leather as a building material has been overtaken by plastic or metal. But its strength and flexibility makes it so versatile.
He uses whole sections of leather for his designs, unlike mass-produced pieces that are generally made from smaller cuts stitched together: “Wrapping a bag in one piece of leather makes it much more durable. Fewer joins mean it’s structurally far stronger,” he says, pointing out a chair.
“Typically, there would be four panels of leather stitched together to create the bucket shape. However, my design is moulded as a single piece. It’s a medieval process called ‘cuir bouilli’ where craftsmen used to make armour by boiling and moulding leather to the shape of a torso.”
Garvan built his “single-form” house as a prototype, which, ideally he would like to roll out commercially as home or studio solutions. It was intended as a “proof of concept” but its snugness and tactility, he says, have also made it a delight to live in.
The modular structure will make it easy to produce different versions with more windows, rooms and a deeper footprint. Picture a row of his homes, each set in its own green plot, and glinting softly against a blue summer sky. It could be fun – and different.
Photography: Ruth Maria Murphy
This article originally appeared in the Autumn/Winter 2021 issue of IMAGE Interiors Magazine. Have you thought about becoming a subscriber? Find out more, and sign up here.